Паяльна станція
Модель Weller WTCP-S, 50 Ват.
Паяльна станція — багатофункціональний настільний паяльний інструмент, спеціально призначений для застосування у галузі електроніки. Дозволяє якісно виконувати паяні з'єднання чутливих електронних компонентів з максимальним дотриманням усіх встановлених для цього технічних регламентів по температурі та тривалості пайки, рівномірності та швидкості нагрівання, розмірам зони нагріву тощо. Також може застосовуватися для виконання паяльних робіт в електротехніці.
Конструктивно складається з одного або декількох паяльних пристроїв, під'єднаних до основного блоку. Цей блок також містить органи керування приладом і засоби індикації. До складу станції входить і ряд допоміжних елементів — фіксатори, штативи, підставки, засоби очищення робочого органу, тощо. В цілому у подібних пристроях намагаються передбачити усе, що може сприяти виконанню якісного та швидкого монтажу та демонтажу електронних компонентів в умовах ручної пайки. Значна увага приділяється зручності користування приладом, що важливо в ситуаціях значного обсягу паяння та при потребі регулярного здійснення паяльних робіт. Це робить паяльні станції оптимальним засобом для професійного застосування в сфері радіомонтажу та ремонту. Зазвичай вони розповсюджені в майстернях з ремонту електроніки, радіолабораторіях, а в окремих випадках і на виробництві. Прості паяльні станції зустрічаються також у побуті, в складі домашніх майстерень.
Конфігурація та оснащення станцій паяльними пристроями можуть значно різнитися відповідно до конкретних потреб та умов застосування. З огляду на це станції інколи поділяються на монтажні та демонтажні.[1] Однак така класифікація є досить умовною, оскільки в багатьох моделях станцій передбачається можливість підключення окремо придбаних додаткових пристроїв за потребою користувача.
Температура робочого органу паяльної станції вільно налаштовується оператором в широкому діапазоні, який типово знаходиться на проміжку від 100 до 480 °C. Станції з температурами вище 500 °C практично не зустрічаються, що робить їх придатними для паяння з використанням виключно м'яких припоїв. Варто зазначити, що окремі паяльні станції мають фіксовану оптимальну робочу температуру без можливості її зміни користувачем.
Поширення паяльних станцій викликано в першу чергу тим, що ручне паяння в галузі електроніки із використанням простих паяльних засобів, перестає відповідати вимогам якості. Тенденції до інтеграції, мініатюризації та здешевлення електронних компонентів для галузі масового виробництва, спричинили підвищення їх вразливості до теплових ушкоджень. Невелику деталь із дрібними зовнішніми виводами дуже легко перегріти з причини малої теплоємності виводів та малої площі розсіювання тепла самої деталі. Те саме стосується струмопровідних доріжок на друкованих платах, які внаслідок перегрівання починають відшаровуватися через руйнування клею, яким вони закріплені.[2] При виготовленні корпусів електронних компонентів усе частіше замість металів та кераміки використовуються спеціальні пластмаси, які є значно дешевшими та більш технологічними, але мають гірші теплові характеристики і погано витримують термоудар.[3] Проблему ускладнює масовий перехід серійного виробництва до застосування безсвинцевих припоїв, які зазвичай мають вищу на декілька десятків градусів температуру плавлення ніж старі припої з вмістом свинцю.[4] Все це наближає температури паяння до небезпечних меж, що накладає додаткові обмеження на тривалість процесу паяння та звужує діапазон припустимих температур.
Недотримання температурного режиму паяння може також погіршити якість паяних з'єднань. Для забезпечення нормального прогрівання і змочування зпаюваних поверхонь, та для досягнення задовільної плинності припою, його температура повинна бути на 30—40 °C вищою ніж його ліквідус. Але з іншого боку, при занадто високих температурах флюс починає перегріватися, що призводить до послаблення або повної втрати його хімічної активності. Як наслідок, спаювані поверхні погано очищуються від окислів і між ними утворюється неякісний електричний контакт. Так зване, «холодне паяння» є найпоширенішим дефектом паяних з'єднань, який до того ж досить важко розпізнати та діагностувати. В подальшому, при роботі обладнання з такою пайкою, між з'єднаними компонентами може спостерігатися ефект нестійкого (мерехтливого) електричного контакту. Така несправність поводиться непередбачувано і створює ряд ускладнень при ремонті.[3] Якщо на спаюваній поверхні присутній метал, що здатний добре розчинятися в припої (наприклад, золоте або срібне покриття), то тривалість процесу паяння також починає відігравати роль. При тривалому нагріванні в рідкий припій потрапляє відчутна кількість розчиненої домішки. В результаті між ними утворюються інтерметалічні сполуки, які зазвичай є крихкими речовинами, що може призвести до погіршення механічних характеристик спаю.[5]
Таким чином, ризики негативних наслідків через недотримання температурного профілю паяння, зростають, що потребує застосування високоточних паяльних пристроїв.
Крім того, усі сучасні електронні компоненти розробляються в першу чергу виходячи з можливостей автоматизованого масового виробництва. Технологія поверхневого монтажу безперервно розвивається, з'являються нові, мініатюрні, типорозміри дискретних елементів та нові типи корпусів мікросхем, зростає щільність розташування деталей. Електричні контакти постійно зменшуються в розмірах і стають важкодоступними, через що вручну такі компоненти стає дуже складно встановити та припаяти.[3]
Найскладнішими для ручного паяння є BGA компоненти, чисельні зовнішні виводи яких розміщуються на нижній, недосяжній ззовні, площині корпусу. Розтоплення припою можливе виключно шляхом наскрізного прогрівання такого компоненту і вимагає особливо обережного та рівномірного підведення тепла. Процес паяння ускладнюється тим, що кульки припою на нижній стороні корпусу створюють потужний перетік тепла на друковану плату і за рахунок цього швидко охолоджуються. Крім того, перевірити якість паяння BGA компоненту без застосування спеціальних технічних засобів (зокрема, рентгенівських камер) практично неможливо. Тому чітке дотримання заданого температурного профілю стає фактично єдиною запорукою якості пайки. BGA мікросхеми все частіше використовуються практично в будь-яких побутових електронних пристроях. Це потребує застосування нових засобів для здійснення ручного паяння, більш споріднених із технологіями групового (безконтактного) нагрівання, задіяними у масовому виробництві електроніки. Саме паяльні станції забезпечують потрібні засоби паяння, до яких відносяться термоповітряні та інфрачервоні нагрівачі.
Головним елементом, який визначає робочі можливості станції, є її паяльний засіб. Для виконання різних операцій існують спеціальні інструменти і станції можуть комплектуватися одночасно декількома з них. До основних пристроїв для здійснення паяння відносяться:
- звичайні паяльники різних типів;
- ультразвуковий паяльник;[6]
- термоповітряний нагрівач (термофен);
- демонтажний паяльний пінцет (термопінцет) — для SMD-компонентів;
- демонтажний помповий паяльник — для компонентів з наскрізним монтажем;
- інфрачервоний нагрівач.
Паяльник є найпоширенішим інструментом станцій і до їх складу можуть входити одразу декілька паяльників різних типів та потужностей. При такій конфігурації відпадає потреба витрачати час на переналагодження єдиного робочого інструмента при необхідності встановлення жала іншої форми або при зміні його температури, що є зручним у випадку великого обсягу робіт. В окремих станціях можуть застосовуватися паяльники спеціалізовані або з нетиповими конструкціями, до яких можна віднести ультразвукові та індукційні паяльники.[6][7]
Входять до складу станцій як інструмент локального (контактного) нагрівання. У порівнянні із звичайними поодинокими паяльниками вони мають низку переваг, до яких можна віднести:
1. Кращі робочі характеристики
- Температуру робочої частини паяльника можна довільно задавати в широкому діапазоні, в залежності від типу використовуваного припою;
- Із певною точністю забезпечується автоматична підтримка заданої температури, не залежно від виконуваних оператором робіт і швидкості охолодження робочої частини паяльника;
- Присутні засоби індикації режиму роботи пристрою, в тому числі із вказанням поточної температури;
- В паяльниках окремих станцій може бути реалізовано технологію ультразвукового паяння;[6][8]
2. Вища якість нагрівального елементу
- Забезпечується довший строк служби за рахунок застосування як керамічних нагрівачів, що мають більший робочий ресурс порівняно з дротяними нагрівачами, так і нагрівачів принципово інших типів (наприклад, в індукційних паяльниках);[7]
- Більш швидке нагрівання та менша тривалість переходу в режим готовності після вмикання (порядку 10-20 сек), особливо у випадку застосування індукційного методу нагрівання;[7]
- Забезпечується вищий ККД паяльника завдяки застосуванню нагрівачів стрижневої конструкції та трубчастих жал;[2]
3. Наявність блоку живлення
- Забезпечується обов'язкова гальванічна розв'язка нагрівального елементу від електромережі. Це унеможливлює ураження спаюваних деталей високою напругою у випадку порушення ізоляції між нагрівачем та жалом. Також зменшується ризик короткого замикання у випадку, якщо спаювані деталі були заземлені;
- Нагрівальний елемент працює на зниженій напрузі (10-30 В), що підвищує безпечність використання та мінімізує шанси раптового пробою ізоляції. Крім того, робота на зниженій напрузі дозволяє значно підвищити як потужність так і довговічність нагрівального елементу. Такий ефект досягається за рахунок використання в його конструкції дроту більшої товщини, що робить неможливим його швидке перегорання;[8]
- Забезпечується заземлення усього пристрою, в тому числі жала паяльника. Це зменшує ризик пошкодження електронних компонентів як статичною електрикою на жалі, так і наведеною на ньому ємнісною паразитною напругою від нагрівального елемента;
- Присутність запобіжника унеможливлює перенавантеження пристрою в аварійних ситуаціях;
4. Більша зручність використання
- Робоча частина паяльника має менші розміри та вагу.[7] Це зменшує втому оператора та дозволяє йому здійснювати більш тонкі і точні дії;
- Конструкцією станції, як її невід'ємна частина, передбачено увесь набір допоміжних засобів для швидкого та якісного здійснення паяння (підставка для жала, засіб очищення жала та ін.);
- В окремих моделях можуть бути реалізовані режими автоматичного вимкнення;
- У деяких паяльних станціях присутні додаткові паяльні пристрої (термофен, помповий паяльник, тощо);
Недоліки:
- Загальна громіздкість паяльної станції унеможливлює її використання у відриві від стаціонарного робочого місця, в тому числі у пересувних умовах;
- Надмірна для багатьох застосувань складність пристрою, яка є не потрібною у більшості звичайних ситуацій: при лудінні металевих поверхонь, та при спаюванні простих деталей: проводів, електричних роз'ємів та різних металевих виробів;
- Як наслідок — завищена вартість.
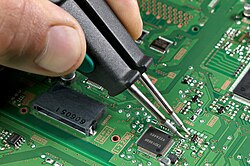
Демонтаж електронних компонентів на друкованій платі становить особливу проблему. В процесі пошуку несправності часто виявляється необхідним відпаювати окремі компоненти, лише з метою діагностики їхнього стану. Це вимагає від процесу демонтажу особливої делікатності, оскільки відокремлені деталі, в разі виявлення їх працездатності, необхідно повернути в початковий стан не погіршивши в результаті їх якості. Деталі із багатьма зовнішніми виводами особливо важко відокремити від плати не пошкодивши їх, і не порушити при цьому оточуючу діляну плати. Для механічного роз'єднання таких деталей потрібно одночасно розтопити припій на усіх паяних контактах, або певним чином почергово видалити цей припій на кожному контакті окремо, що в будь-якому разі становить нетривіальну задачу. Існує багато методик здійснення демонтажу електронних компонентів і для цього створено багато супутніх засобів: ручні механічні помпи для припою, мідні плетені стрічки (англ. solder wick або solder braid), жала для паяльників спеціальної форми, тощо. Для застосування в паяльних станціях обираються максимально ефективні та зручні засоби, використання яких найбільше виправдане у професійній діяльності при регулярних ремонтних роботах.
До таких засобів відносяться:
- Паяльний пінцет (термопінцет) являє собою два малопотужних паяльника, розміщених на спільній поперечній осі. Спеціально призначений для відпаювання дискретних компонентів поверхневого монтажу що мають два виводи (SMD-резистори, діоди, конденсатори, тощо). Дозволяє здійснювати швидкий та максимально акуратний демонтаж, створюючи при цьому мінімальний вплив на оточуючі ділянки друкованої плати.[2] Існують чисельні варіації паяльних пінцетів, в тому числі моделі, що мають кінцівки спеціальної форми. Це дає змогу демонтувати за їх допомогою деякі багатовивідні компоненти з поверхневим монтажем, в тому числі мікросхеми.
- Помповий паяльник має трубчасте жало і, зазвичай, виконується у формі пістолета. За командою оператора, через жало паяльника втягується потік повітря, завдяки вбудованому в основний блок станції компресору. В пістолеті розміщено резервуар для утримання припою, який потрібно періодично очищувати. Такий засіб є найкращим інструментом для демонтажу мікросхем в DIP корпусах та дискретних наскрізних компонентів.[9][10] Спочатку трубчасте жало одягається на припаяний вивід деталі і розтоплює припій, після цього, потік повітря всмоктує рідкий припій в резервуар і охолоджує зону пайки. Видалення припою здійснюється почергово на кожному окремому виводі деталі, забезпечуючи максимально повне очищення її металевих контактів і отворів, в які вона встановлена. В результаті, електронний компонент може бути вільно вилучений з друкованої плати не пошкоджуючи струмопровідних доріжок, контактних майданчиків та металізованих отворів. Крім того, такий паяльник дозволяє легко знімати надлишковий припій з довільних ділянок паяння, що дозволяє застосовувати його у широкому колі робіт: для демонтажу роз'ємів і провідників, для очищення контактів, тощо.[10] Даний пристрій є дуже специфічним і, як правило, входить до складу тільки окремих демонтажних паяльних станцій. Деякі помпові паяльники спеціально призначені для відокремлення компонентів з поверхневим монтажем. Для них передбачено можливість встановлення різних насадок, відповідно до розмірів мікросхем. Режим всмоктування повітря використовується для утримання мікросхеми та зняття її з плати.
- Засоби групового (безконтактного) нагрівання використовуються для демонтажу багатовивідних компонентів, як правило мікросхем, зібраних за технологією поверхневого монтажу. До таких засобів відносяться термоповітряні та інфрачервоні нагрівачі.

Термоповітряні станції використовують для нагрівання відкритий потік гарячого повітря, якій фокусується на потрібній ділянці за допомогою сопла та спеціальних насадок. Принцип роботи такого пристрою аналогічний звичайному побутовому фену з тією різницею, що температура вихідного потоку є значно вищою і може вільно обиратися оператором в широкому діапазоні. Зазвичай, типові термофени здатні забезпечувати температури повітря в межах від 100 до 480 °C.[4]
Конструктивно подібні станції складаються з маніпулятора-термофену та основного блоку, до якого він під'єднаний. Нагрівання потоку повітря відбувається в самому маніпуляторі за допомогою спіралеподібного або керамічного нагрівача. Формування потоку повітря може здійснюватися різними методами, відповідно до яких станції поділяються на:
- Компресорні, в яких подача повітря відбувається за допомогою діафрагмового компресора, розташованого в основному блоці станції;
- Турбінні, де маніпулятор термофену має вбудований малогабаритний безшумний електродвигун з крильцями, який створює потрібну величину повітряного потоку.[11][2][4]
На практиці, основна відмінність між цими двома типами полягає в тому, що турбінні станції за нормальних умов, зазвичай, здатні формувати більший потік повітря, але при цьому забезпечують менший тиск. В результаті, станції з компресорами краще працюють у випадках, коли потік повітря змушений проходити крізь вузькі отвори або тонкі трубки, наприклад, при застосуванні насадок.[2]
Регулювання величини потоку повітря та його температури на виході з сопла, може здійснюватися в кожній станції по своєму. У найпростішому випадку станція може взагалі не мати термодатчика, через що зворотній зв'язок за температурою в ній виявляється відсутнім. Оператор такої станції може оцінити теплову картину на місці паяння лише приблизно, спостерігаючи за положенням регуляторів та поведінкою припою. Сфера використання подібних термофенів, зазвичай, обмежується лише демонтажними операціями. У найбільш досконалих станціях реалізовано термостабілізацію. Вони здатні вимірювати температуру на виході термофену і відображати її на екрані. Також в них може бути передбачено барометричний датчик потоку повітря.[4]
Струменем повітря дуже важко досягти одночасного та рівномірного прогрівання поверхні великої площі. У місці найпершого контакту нагрітого повітря з поверхнею, її температура завжди є найвищою. По мірі розтікання струменя, температура прилеглих ділянок поверхні швидко падає за рахунок утворення турбулентних вихорів, які погано притискаються до поверхні, що заважає їм віддавати тепло. В результаті, раніше нагріті зони встигають частково охолонути і їх потрібно нагрівати знову. Можна спробувати вирішити цю проблему шляхом зниження швидкості струменя повітря до того рівня при якому турбулентність не виникає. В такому випадку прогрівання стає більш рівномірним, але при цьому падає потужність теплового потоку і поверхня отримує менше тепла.[4]
З огляду на це, для боротьби з вихорами у багатьох станціях застосовується технологія Vortex, за допомогою якої на виході сопла формується закручений потік повітря. Також конструкцією, зазвичай, передбачається можливість встановлення на термофен різноманітних змінних насадок. Вони дозволяють змінювати форму потоку повітря і локалізувати його розповсюдження відповідно до умов здійснення паяння. Мікросхеми різних типів та розмірів потребують окремих спеціальних насадок. Перед початком паяння, деякі насадки повинні бути відповідним чином закріплені на платі та підлаштовані під мікросхему.
При здійсненні демонтажу компонентів плати, необхідно слідкувати за розповсюдженням потоку нагрітого повітря. Якщо в зоні, прилеглій до ділянки демонтажу, розміщено теплочутливі компоненти (наприклад, електролітичні конденсатори або вироби з пластмаси) — існує ризик їх випадкового перегрівання, що може їх пошкодити, скоротити строк служби або взагалі вивести з ладу. Монтаж SMD-компонентів із застосуванням термофену ускладнюється тим, що створюваний ним потік повітря в процесі паяння може легко зсунути дрібні, погано закріплені компоненти. З боку користувача це потребує вживання додаткових запобіжних заходів. Реалізована в окремих станціях технологія Vortex дозволяє частково вирішити цю проблему.
Термофени, в цілому, справляються із завданнями паяння мікросхем малих та середніх розмірів, наприклад, при ремонті плат портативних пристроїв, в тому числі стільникових телефонів.[4]

Паяльні станції з інфрачервоними (ІЧ) нагрівачами можна виділити в окрему групу, оскільки вони конструктивно сильно відрізняються від усіх інших. Подібні пристрої дозволяють здійснювати високоточне паяння, процес якої у значній мірі наближається до умов, створюваних обладнанням масового виробництва електроніки. При цьому, паяння може відбуватися із довільно заданим розподілом температур у часі (температурним профілем), який підбирається у відповідності до рекомендацій виробників електронних компонентів. Це мінімізує ризики теплового удару та пошкодження спаюваних деталей, а також дозволяє уникнути значного перепаду температур в процесі паяння, що могло б спричинити появу деформацій.
В ІЧ станціях основним механізмом передачі тепла є інфрачервоні електромагнітні хвилі середнього діапазону з довжинами 2—10 мкм.[4][3] Вибір такого діапазону викликаний тим, що випромінення в ньому має найкращі показники поглинання енергії. Більш короткі хвилі, що належать до ближньої інфрачервоної області спектру (0,7—1,5 мкм), є малопридатними до застосування в пайці, оскільки поверхні різних кольорів нагріваються ними нерівномірно: темніші поверхні перегріваються, а блискучі ділянки прогріваються недостатньо. Крім того, для короткохвильового ІЧ випромінення властиві явища затінення, що додатково посилює неоднорідність температури. З іншого боку, дальня область ІЧ спектру (6—1000 мкм) взагалі не може використовуватися для паяння, оскільки не дозволяє розвинути потрібні для плавлення припою температури.[3] Теплове випромінення, застосоване в ІЧ станціях, забезпечує достатню для якісного паяння рівномірність нагрівання усіх елементів поверхні, навіть за умови наявності у них різної відбивальної здатності.
Для випромінення ІЧ хвиль середнього діапазону, в паяльних станціях використовуються спеціальні лампи розжарення разом з системою дзеркал. При цьому як джерело тепла можуть виступати трубчасті нагрівачі різних типів, до яких відносяться:[9][3]
- Керамічні нагрівачі, які мають вищу надійність та довговічність у порівнянні з кварцовими. Їх випромінення в основному має довжини хвиль в діапазоні 3—10 мкм і не містить оптично видимої складової;
- Кварцові нагрівачі, що випромінюють ІЧ хвилі з довжинами 1,3—3 мкм, а також видиме світло. Вони розігріваються швидше ніж керамічні і формують більш однорідну зону нагрівання.[12]
Нагрівачі інколи можуть бути об'єднані в панелі відносно великих розмірів, з температурою випромінюючої поверхні близько 280–320 °C. В таких пристроях, нагрівання спаюваних об'єктів здійснюється на 60% за рахунок звичайної конвекції і на 40% — шляхом поглинання середньохвильового ІЧ випромінення.[3]
У малопотужних станціях найпростішої конструкції робочим органом може бути ІЧ гармата. Вона являє собою ручний інструмент, оснащений випромінювачем, який під'єднується до основного блоку станції. Гарматою можна вільно маніпулювати, або за потребою, встановлювати її на вертикальний штатив.
Більш досконалі станції мають стаціонарний верхній нагрівач та термостіл, який дозволяє зафіксувати плату і за потребою здійснює нагрівання її нижньої частини за допомогою окремого ІЧ випромінювача. При його роботі в парі з основним (верхнім) випромінювачем, забезпечується прогрівання плати з двох поверхонь одночасно, що сприяє однорідності температур і знижує теплові деформації. Такий підхід особливо корисний при пайці BGA мікросхем, оскільки за рахунок цього знижується відтік тепла з нижньої частини мікросхеми, яка контактує з платою. В результаті, температуру верхнього нагрівання можна зменшити і тим самим мінімізувати ризик теплового пошкодження мікросхеми. Термостіл виконує попередній прогрів усієї плати до температури 100–150 °С, а вже після цього починається паяння самої BGA мікросхеми основним випромінювачем.
У найдосконаліших станціях додатково передбачаються засоби примусового охолодження спаюваних деталей (вентилятори), а також дистанційні ІЧ термодатчики, які здійснюють одночасний контроль температури на різних ділянках нагрівання. При цьому, може бути реалізовано декілька незалежно контрольованих температурних зон. Станції також можуть мати засоби моніторингу та керування за допомогою персонального комп'ютера (зазвичай, через інтерфейс RS-232), функції звукового сповіщення, тощо.
Площа та форма зони нагрівання ІЧ станції може бути тонко налаштована під кожну конкретну задачу. Для цього основний випромінювач обладнується спеціальними шторками, які дозволяють змінювати розміри вихідного отвору лампи, а ті ділянки плати, нагрівання яких є небажаним, можуть бути екрановані за допомогою тепловідбиваючої фольги.[4]
В цілому, у порівнянні з термофенами, ІЧ станції забезпечують найбільш контрольований та акуратний режим рівномірного нагрівання поверхонь великої площі. Тому їх застосування максимально виправдане у випадках паяння мікросхем з великими розмірами корпусів (наприклад, при ремонті материнських плат та карт розширення комп'ютерів),[4] та при здійсненні групового (безконтактного) паяння значної кількості SMD-компонентів.
Недоліки ІЧ станцій:
- Технологія паяння із застосуванням ІЧ випромінювання є найбільш придатною до використання у сфері електроніки де розповсюджені елементи поверхневого монтажу. Електронні компоненти для наскрізного монтажу потребують інших засобів паяння.[3] Однак, при необхідності, ІЧ станціями можна паяти і наскрізні компоненти.[4]
- Не зважаючи на вжиті заходи, актуальною залишається проблема залежності ступеня поглинання енергії ІЧ випромінення від поглинаючої здатності матеріалів, з яких виготовлені спаювані компоненти. В результаті, нагрівання поверхонь та окремих частин кожного спаюваного елементу є дещо нерівномірними, через різну спектральну чутливість матеріалів.[3]
- ІЧ станції є спеціалізованими пристроями, і в багатьох випадках у них взагалі не передбачені додаткові паяльні засоби та допоміжні елементи (паяльник, термофен, тощо). Такі станції можуть розглядатися лише як корисне доповнення до класичних паяльних інструментів, які необхідно мати окремо.
- Вартість ІЧ паяльних станцій зазвичай є в декілька разів вищою ніж у термоповітряних.[4]
- ↑ Ісаєв Олександр. Как работать с SMD и кому нужна паяльная станция? [Як працювати з SMD і кому потрібна паяльна станція?]. www.qrz.ru (російською) . Архів оригіналу за 29 серпня 2013. Процитовано 12 серпня 2013.
- ↑ а б в г д DI HALT (19 березня 2011). Трактат о паяльниках. Easy Electronics електроніка для усіх (російською) . Архів оригіналу за 29 серпня 2013. Процитовано 12 серпня 2013.
- ↑ а б в г д е ж и к Медведєв А.М. (2007). Сборка и монтаж электронных устройств [Збірка та монтаж електронних пристроїв]. Мир электроники (російською) . Москва: Техносфера. ISBN 978-5-94836-131-4.
- ↑ а б в г д е ж и к л м SiriusTeam (18 грудня 2009). Горячий воздух или ИК излучение? Выбор паяльной станции [Гаряче повітря або ІЧ випромінення? Вибір паяльної станції.]. gsmeducation.ru (російською) . компанія "Сіріус-Телеком". Процитовано 12 серпня 2013.
{{cite web}}
: Обслуговування CS1: Сторінки з параметром url-status, але без параметра archive-url (посилання) - ↑ Говард Г. Манко (1968). Пайка и припои. Материалы, конструкции, технология и методы рассчёта [Паяння та припої. Матеріали, конструкції, технологія та методи розрахунку] (російська) . Москва: Машиностроение.
- ↑ а б в USS-9200 ультразвуковая паяльная система [USS-9200 ультразвукова паяльна система]. www.argus-x.ru (російською) . компанія ARGUS X. Архів оригіналу за 29 серпня 2013. Процитовано 12 серпня 2013.
- ↑ а б в г Колесов, Дмитро. Паяльники с индукционным нагревом: смена поколений [Паяльники з індукційним нагріванням: зміна поколінь]. www.kit-e.ru. "Компоненти і технології" №6 (російською) . Архів оригіналу за 29 серпня 2013. Процитовано 12 серпня 2013.
- ↑ а б Віноградов Н.В. (1970). Производство электрических машин [Виробництво електричних машин] (російська) . Москва: Энергия.
- ↑ а б Стахняк Юрій. Как выбрать паяльную станцию [Як обрати паяльну станцію]. www.goot.com.ua (російською) . Masteram. Архів оригіналу за 29 серпня 2013. Процитовано 12 серпня 2013.
- ↑ а б Rework and Repair For Electronics [Відео урок з ремонту електроніки]. YouTube. урок №4 (англійською) . PACE inc. Процитовано 12 серпня 2013.
- ↑ Термовоздушная паяльная станция [Термоповітряна паяльна станція]. www.go-radio.ru (російською) . Архів оригіналу за 29 серпня 2013. Процитовано 12 серпня 2013.
- ↑ Кварцевые инфракрасные излучатели [Кварцові інфрачервоні випромінювачі]. www.elcer.com.ua (російською) . ИНТМАКС. Архів оригіналу за 29 серпня 2013. Процитовано 12 серпня 2013.
- Rework and Repair For Electronics [Відео урок з ремонту електроніки]. YouTube. урок №3 (англійською) . PACE inc. Процитовано 12 серпня 2013.
- [http://www.youtube.com/watch?v=e8KRPFOD1RE Rework and Repair For Electronics [Відео урок з ремонту електроніки]. YouTube. урок №4 (англійською) . PACE inc. Процитовано 12 серпня 2013.]Rework and Repair For Electronics [Відео урок з ремонту електроніки]. YouTube. урок №4 (англійською) . PACE inc. Процитовано 12 серпня 2013.
- Паяльна станція. Детальний опис